Since its establishment our company is engaged in supplying special and unique production equipment and production lines for enterprises of aeronautical and space industries. We are well aware of the needs and requirements of the industry enterprises and offer efficient solutions to a wide range of preforming, machining and modular assembly processes.
MIRROR MILLING EQUIPMENT AND TECHNOLOGY
DUFIEUX INDUSTRIE suggested an effective method for mechanical treatment of panels. This method patented by DUFIEUX INDUSTRIE is essentially an alternative green technology as compared with the legacy process used until now.
The up-to-date mirror milling technology offers substantial technical, economical and ecological advantages for panel machining. Mirror milling is an optimum solution for reducing weight of the entire panel group, the need for such technology arose to a large extent from more stringent environmental protection requirements. Such advanced technology developed for said purposes by DUFIEUX INDUSTRIE is called Mirror Milling System (MMS). It is implemented in the PERFORM MMS 8008 and 8228 panel machining complexes.
The PERFORM MMS complex serves the following functions:
- Positioning at “zero point,” clamping of panels during machining.
- Identification of the panel and measurement of its position and actual shape.
- Correction (where necessary) of the theoretical machining program.
- Machining of pockets, milling and drilling.
The PERFORM MMS complex includes two vertical cross arms located opposite each other and moving in the longitudinal direction. Each cross arm has a five-axis controlled working head with a horizontally positioned spindle.
The first cross arm is used for milling performed with the aid of an electrically-driven spindle. It treats the internal panel surface and is intended for pocket machining, drilling and part profile machining (see the Figure).
The second cross arm is used to hold the machined panel. It has no spindle but is outfitted with a single-sided load-bearing support to hold the panel in the preset position. The second cross arm moves and rotates in much the same manner as the first cross arm. Programmable movement of the second cross arm is symmetrical to the movement of the first cross arm.
The PERFORM MMS complex design precludes any deformation of the machined panels when they are clamped and machined.
Appui – Load-bearing support (absorbs load and vibration affecting the panel).
Outil Coupant – Cutting tool.
Panneau – Machined panel.
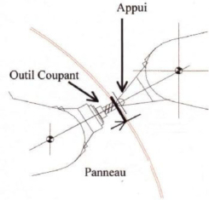
The machining process includes the following stages:
- Preparation of the panel for machining.
- Loading panels into pallets (clamping the machined panel in the frame with a flexible arrangement system using telescopic stops and flexible clamps).
- Panel transportation to the machining zone.
- Panel scanning by a laser measurement system.
- Panel machining.
- Unloading the panel after machining.
- Quality inspection after machining.
Main advantages of mirror milling as compared with chemical milling are as follows:
- Machining time substantially reduced by 50% (for example, it takes 10 hours to machine this panel using chemical milling or 4 hours 40 minutes using mirror milling).
- Production cost reduced by 50%.
- No need for protection of the production process against harmful chemical components and subsequent processing and utilization of such components.
Illustrations for machining process stages
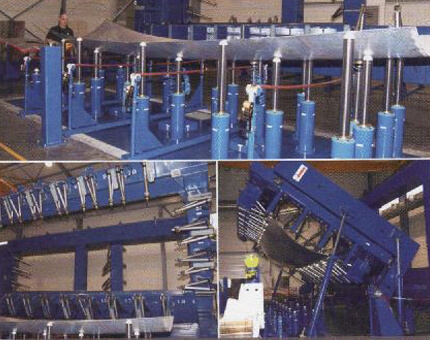
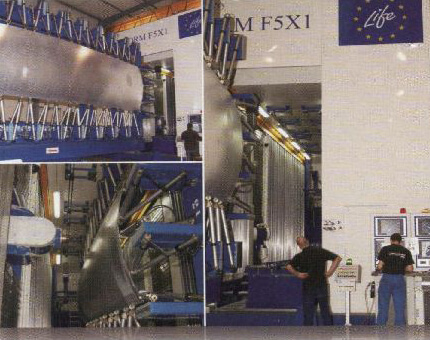
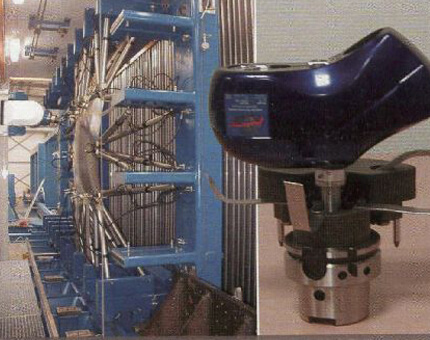
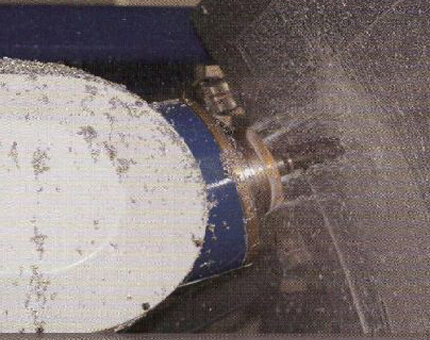
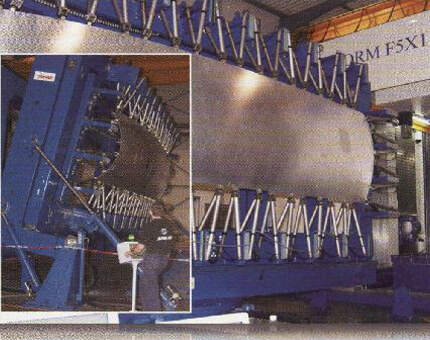
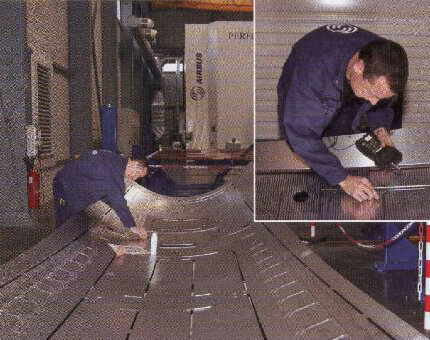
Aerolia (Saint-Nazaire, France) is a 1st level AIRBUS supplier. Its plant operates seven MMS machines (the first machine was commissioned in 2005). Currently, Aerolia has produced more than 30,000 skins for off-the-shelf products. Successful use of the MMS technology allowed Aerolia to refuse chemical milling altogether.
Application Results
Aerolia (Saint-Nazaire, France) is a 1st level AIRBUS supplier. Its plant operates seven MMS machines (the first machine was commissioned in 2007). Currently, Aerolia has produced more than 30,000 skins for off-the-shelf products.
Successful use of the MMS technology allowed Aerolia to:
- completely refuse chemical milling of the skins manufactured in the territory of France;
- manufacture 8,000 off-the-shelf skins per annum;
- reduce the amount of defective products to 0;
- arrange for three-shift work;
- bring up the utilization factor to 98 – 99%;
- use three persons per shift.

AVIATION
CONSULTING -
TECHNO CJSC
Энергия совместных решений
129164, Russia, Moscow, st. Yaroslavskaya, 8, building 5, office 318
Tel.: +7 (495) 626-5471
Fax: +7 (495) 626-5472
E-mail: aviacons@aviacons.ru